Отжиг сталей
Отжиг титановых сплавов
Нормализация
Закалка сталей
Отпуск сталей
Старение
Обработка холодом
Цементация стали
Цианирование и нитроцементация
Азотирование стали
Ток высокой частоты (ТВЧ)
Пескоструйная обработка металлов
ТЕРМИЧЕСКАЯ ОБРАБОТКА МЕТАЛЛА
Наша фирма предлагает Вам следующие улуги: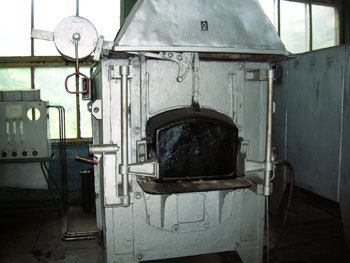
Термообработка металлов включает такие процессы как: закалка, отжиг, старение, отпуск. В зависимости от таких факторов, как температура нагревания, время выдержки и скорость охлаждения, металл может претерпевать различные структурные изменения. Как правило, термообработка металлов может сочетаться и с другими способами воздействия.
Термообработка металлических деталей проводится в тех случаях, когда необходимо либо повысить прочность, твердость, износоустойчивость или упругость детали или инструмента, либо, наоборот, сделать металл более мягким, легче поддающимся механической обработке.

Закалка стальных деталей
Закалка придает стальной детали большую твердость и износоустойчивость. Для этого деталь нагревают до определенной температуры, выдерживают некоторое время, чтобы весь объем материала прогрелся, а затем быстро охлаждают в масле (конструкционная и инструментальная сталь) или воде (углеродистая сталь).Обычно детали из конструкционных сталей нагревают до 880—900° С (цвет каления светло-красный), из инструментальных—до 750—760° С (цвет темно-вишнево-красный), а из нержавеющей стали—до 1050—1100° С (цвет темно-желтый). Нагревают детали вначале медленно (примерно до 500° С), а затем быстро. Это необходимо для того, чтобы в детали не возникли внутренние напряжения, что может привести к появлению трещин и деформации материала.
Применяют в основном охлаждение в одной среде (масло или вода), оставляя в ней деталь до полного остывания. Однако этот способ охлаждения непригоден для деталей сложной формы, в которых при таком охлаждении возникают большие внутренние напряжения. Детали сложной формы сначала охлаждают в воде до 300—400° С, а затем быстро переносят в масло, где и оставляют до полного охлаждения. Время пребывания детали в воде определяют из расчета: 1с на каждые 5—6 мм сечения детали. В каждом отдельном случае это время подбирают опытным путем в зависимости от формы и массы детали.
Качество закалки в значительной степени зависит от количества охлаждающей жидкости. Важно, чтобы в процессе охлаждения детали температура охлаждающей жидкости оставалась почти неизменной, а для этого масса ее должна быть в 30—50 раз больше массы закаливаемой детали. Кроме того, перед погружением раскаленной детали жидкость необходимо тщательно перемешать, чтобы выровнять ее температуру по всему объему.
В процессе охлаждения вокруг детали образуется слой газов, который затрудняет теплообмен между деталью и охлаждающей жидкостью. Для более интенсивного охлаждения деталь необходимо постоянно перемещать в жидкости во всех направлениях.
Небольшие детали из малоуглеродистых сталей (марки «30», «35», «40») слегка разогревают, посыпают железосинеродистым калием (желтая кровяная соль) и вновь помещают в огонь. Как только обсыпка расплавится, деталь опускают в охлаждающую среду. Железосинеродистый калий расплавляется при температуре около 850° С, что соответствует температуре закалки этих марок стали.
Отпуск закаленных деталей
Отпуск закаленных деталей уменьшает их хрупкость, повышает вязкость и снимает внутренние напряжения. В зависимости от температуры нагрева различают низкий, средний и высокий отпуск.
Низкий отпуск применяют главным образом при термообработке измерительного и режущего инструмента. Закаленную деталь нагревают до температуры 150—250° С (цвет побежалости—светло-желтый), выдерживают при этой температуре, а затем охлаждают на воздухе. В результате такой обработки материал, теряя хрупкость, сохраняет высокую твердость и, кроме того, в нем значительно снижаются внутренние напряжения, возникающие при закалке.
Средний отпуск применяют в тех случаях, когда хотят придать детали пружинящие свойства и достаточно высокую прочность при средней твердости. Для этого деталь нагревают до 300—500° С и затем медленно охлаждают.
И наконец, высокому отпуску подвергают детали, у которых необходимо полностью снять все внутренние напряжения. В этом случае температура нагрева еще выше 500—600° С.
Термообработка металлов в виде деталей простой формы (валики, оси, зубила, кернеры) часто делается за один раз. Нагретую до высокой температуры деталь опускают на некоторое время в охлаждающую жидкость, затем вынимают. Отпуск происходит за счет тепла, сохранившегося внутри детали.
Небольшой участок детали быстро зачищают абразивным брусочком и следят за сменой цветов побежалости на нем. Когда появится цвет, соответствующий необходимой температуре отпуска (220° С— светло-желтый, 240° С—темно-желтый, 314° С—светло-синий, 330° С— серый), деталь вновь погружают в жидкость, теперь уже до полного охлаждения. При отпуске небольших деталей (как и при закалке) нагревают какую-нибудь болванку и на нее кладут отпускаемую деталь. При этом цвет побежалости наблюдают на самой детали.
Отжиг стальных деталей
Чтобы облегчить механическую или пластическую обработку стальной детали, уменьшают ее твердость путем отжига. Так называемый полный отжиг заключается в том, что деталь или заготовку нагревают до температуры 900° С, выдерживают при этой температуре некоторое время, необходимое для прогрева ее по всему объему, а затем медленно (обычно вместе с печью) охлаждают до комнатной температуры.
Внутренние напряжения, возникшие в детали при механической обработке, снимают низкотемпературным отжигом, при котором деталь нагревают до температуры 500—600° С, а затем охлаждают вместе с печью. Для снятия внутренних напряжений и некоторого уменьшения твердости стали применяют неполный отжиг — нагрев до 750—760° С и последующее медленное (также вместе с печью) охлаждение.
В термообработке отжиг используется также при неудачной закалке или при необходимости перекаливания инструмента для обработки другого металла (например, если сверло для меди нужно перекалить для сверления чугуна). При отжиге деталь нагревают до температуры несколько ниже температуры, необходимой для закалки, и затем постепенно охлаждают на воздухе. В результате закаленная деталь вновь становится мягкой, поддающейся механической обработке.
Отжиг и закаливание дюралюминия
Отжиг дюралюминия производят для снижения его твердости. Деталь или заготовку нагревают примерно до 360° С, как и при закалке, выдерживают некоторое время, после чего охлаждают на воздухе.
Твердость отожженного дюралюминия почти вдвое ниже, чем закаленного.
Приближенно температуру нагрева дюралюминиевой детали можно определить так. При температуре 350—360°С деревянная лучина, которой проводят по раскаленной поверхности детали, обугливается и оставляет темный след. Достаточно точно температуру детали можно определить с помощью небольшого (со спичечную головку) кусочка медной фольги, который кладут на ее поверхность. При температуре 400° С над фольгой появляется небольшое зеленоватое пламя.
Отожженный дюралюминий обладает небольшой твердостью, его можно штамповать и изгибать вдвое, не опасаясь появления трещин.
Дюралюминий можно подвергать термообработке (закаливанию). При закаливании детали из этого металла нагревают до 360—400° С, выдерживают некоторое время, затем погружают в воду комнатной температуры и оставляют там до полного охлаждения. Сразу после этого дюралюминий становится мягким и пластичным, легко гнется и куется. Повышенную же твердость он приобретает спустя три-четыре дня. Его твердость (и одновременно хрупкость) увеличивается настолько, что он не выдерживает изгиба на небольшой угол.
Наивысшую прочность дюралюминий приобретает после старения. Старение при комнатных температурах называют естественным, а при повышенных температурах - искусственным. Прочность и твердость свежезакаленного дюралюминия, оставленного при комнатной температуре, с течением времени повышается, достигая наивысшего уровня через пять-семь суток. Этот процесс называется старением дюралюминия.
Отжиг меди и латуни
Термообработка меди позволяет сделать металл более мягким, либо более твердым. Однако в отличие от стали закалка меди происходит при медленном остывании на воздухе, а мягкость медь приобретает при быстром охлаждении в воде. Если медную проволоку или трубку нагреть докрасна (600°) на огне и затем быстро погрузить в воду, то медь станет очень мягкой. После придания нужной формы изделие вновь можно нагреть на огне до 400° С и дать ему остыть на воздухе. Проволока или трубка после этого станет твердой.
Если необходимо выгнуть трубку, ее плотно заполняют песком, чтобы избежать сплющивания и образования трещин.
Отжиг латуни позволяет повысить ее пластичность. После отжига латунь становится мягкой, легко гнется, выколачивается и хорошо вытягивается. Для отжига латунь нагревают до 500° С и дают остыть на воздухе при комнатной температуре.
Воронение стали
После воронения стальные детали приобретают черную или темно-синюю окраску различных оттенков, они сохраняют металлический блеск, а на их поверхности образуется стойкая оксидная пленка; предохраняющая детали от коррозии. Перед воронением изделие тщательно шлифуют и полируют. Поверхность его обезжиривают промывкой в щелочах, после чего изделие прогревают до 60— 70° С. Затем помещают его в печь и нагревают до 320—325° С. Ровная окраска поверхности изделия, получается только при равномерном его прогреве. Обработанное таким образом изделие быстро протирают тряпкой, смоченной в конопляном масле. После смазки изделие снова слегка прогревают и вытирают насухо.
Стальным деталям можно придать красивый синий цвет. Для этого составляют два раствора: 140г. гипосульфита на 1л. воды и 35г. уксуснокислого свинца («свинцовый сахар») также на 1л. воды. Перед употреблением растворы смешивают и нагревают до кипения. Изделия предварительно очищают, полируют до блеска, после чего погружают в кипящую жидкость и держат до тех пор, пока не получат желаемого цвета. Затем деталь промывают в горячей воде и сушат, после чего слегка протирают тряпкой, смоченной касторовым или чистым машинным маслом. Детали, обработанные таким способом, меньше подвержены коррозии.
Наша организация выполнит любые виды работ по термообработке стальных изделий в Киеве, а именно: термообработка стали, термообработка алюминия, термообработка алюминиевых сплавов, термообработка меди, термообработка латуни, термообработка титановых сплавов, ТВЧ, азотирование, цианирование и нитроцементация, цементация, обработка холодом, старение